Conversation with Ashtad Engineer
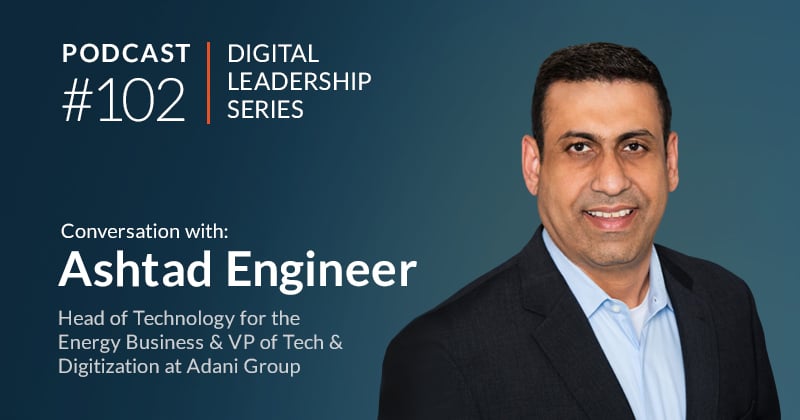
Good day and welcome to episode 102 of our Digital Leadership Podcast, produced by, for, and about digital industry leaders. Today I am pleased to introduce Ashtad Engineer, Head of Technology, Energy, and VP of Tech and Digitization at the Adani Group, a $12 billion infrastructure conglomerate with interests in ports and logistics, power generation and transmission, renewable energy, gas distribution, and agricultural products. Ashtad is a lifelong digital industry leader having led strategic sales and partner ecosystems at my alma mater Wonderware, during its ownership by Invensys and later Schneider Electric. Prior, he led the SAP manufacturing systems practice for Tata Consulting Services and worked in consulting with Rockwell Automation.
Ashtad, welcome to our Digital Industry Leadership Podcast.
Thank you very much Ken, I appreciate it. Very excited to be here.
You and I go back quite a way, so it’s well past the time to have you on this, and I appreciate the fact that we’re finally able to pull it together.
So, first of all, since I often mention that Momenta loves engineers, I have to greatly appreciate anyone who features this as part of their proper name, so for whatever part you had in actually taking that as a proper name, well done! But let’s start with your professional journey, tell us a bit about your background, and how it has informed your views of digital industry.
I would say my journey is like an S95 model! And the reason I chose the S95 model is, starting from control systems I’m really fascinated on how real-time control works during the PLC days, understanding how machines work, and then being able to see that working, and the whole boom of software coming in the late nineties, and early 2000’s, propelled the thinking of what happens to information after its generated at that level? Okay, let’s see what happens a level above. This whole operations management space started to become very interesting, because now you could start to understand how decisions are made, how things are made, and the processes that go into that.
Then when you go onto the top you actually have an understanding of the business processes, and the whole shop to top has been I would say close to 25 years I’ve been in the industry, it’s constant throughout. So, digital today is just an accelerator I would say, but I think the fundamental things about the processes and its associated planning, control, execution, and closing off the loop. If you look at the background of closing the loop in terms of sense and response and being able to do that, the closing of the loop happens at every step in the enterprise, right from the control systems, to operations management, and then to the business systems, you’ve got a planning component, you’ve got an execution component, and you’ve got a feedback controlled component. Today, digitization is all about bringing that together on a converging path, to be able to solve business outcomes and challenges. I often sometimes say that having the name and the degree allows me to see things in a holistic manner.
I love that. I guess looking at your formal education, and great control systems education as it is, and then of course all the work you’ve done in large leaders if you will, in industrial automation and control systems; what inspired you to come into this space early-on?
My father is a very well-respected individual in the whole design and electronics R&D space, so seeing my father right from childhood putting it out there in terms of technology, that excited me, and the whole thing about science on the why aspect of why the thing works the way it works, that got me thinking into taking on the control systems aspect. It was necessarily exciting that things which you can do, the results are immediately seen.
So for example, when I was programming my first PLC, you could actually see an embedded control working, and you can actually see your logic not working in a virtualized environment, like you have run times on visual studio, where you run and compile a project. But when you actually take a PLC and program it, and that got me thinking about the control systems, because in college and all of that we had the very first generations of Rockwell, Alan Bradley, and we tinkered with that. So, that got me fascinated into real-time control.
I remember one of my first control systems experiences, this was at Lockheed Own Space, and it was a large processing facility, and literally we set up a Wonderware system, we put a touchscreen on it, it was talking with the PLC. I had somebody come in and actually try it, he hits the button on it, and the color didn’t change on it because we hadn’t got that far in the program! Literally there’s this 500-horsepower motor that you can hear off in the distance, winding up. He hits it again and he hits it again, (makes noise) of course it finally blows a breaker on it. But you realize the power when the atomic meets the digital if you will, and how these things come together. So, I laugh, and maybe this is the old guy in me, I laugh when people show me, ‘Hey look, I’m blinking the light on Arduino over the internet’, ‘Well, let me tell you my story son!’
That power inspired me, as it sounds like it did you as well, and lot of that came out of early days at Wonderware, so I was there along with one of our advisory partners, Jesse DeMesa, back in the early nineties actually, when the company were pre-IPO and just about 100 people. I think they were arguably the first significant company to drive what’s called the integration of the information technology, and operational technology, IT and OT, together via this human machine interface they called it at the time, a product called Intouch. How did you see this market leadership continuing, you were there almost 10 years with them I believe?
Yes, it’s like Wonderware is to the OT world as SAP is to IT world. Every control engineer if you’re not from Wonderware it’s like, ‘What?’ Wonderware was a part and parcel of the controls engineer’s toolkit. The whole visualization, I compare this to Apple, you’ve got Apple phones, but the whole systemic user interface designed which Wonderware created, it was the Apple of manufacturing of the user interface. You call it HMR, you call it whatever name you want to, but it’s the wholly human systemic interaction which made it easy for operations, and operations is such a crucial aspect today of any organization, be it manufacturing, be it infrastructure operations.
So, I think the leadership edition maintained by Wonderware was out of the box thinking, and the whole concept of modelling your assets in real-time, and contextualizing. Today, people understand the whole context and contextualization of data, the whole thing propelled where you were able to contextualize in just data on a model, and it pioneered that with their user interface. I think that leadership position today is unmatched in the industry. During my time there acquisitions were made, but the most notable acquisition was of a workflow product. If you see mid-2000 and the end, it all started becoming workflow. Now the whole aspect of business workflows as you know, PPNN and all that stuff at the enterprise layer, but manufacturing and operations required something where you had human systemic interaction, and what better as to complement the operations management system with a human systemic workflow, where the operations guys could actually interact with different systems, with the channels and the forms of communications which they’re already used to.
Like for example, Outlook, you could create workflows right into your Outlook mailbox, or you could take workflows operations management workflows and push it out to the channels like the chat channels. So, that propelled a new way of information management, especially in the operation space. If you look at today and to 10 years back, operations modelling has always been an after part, so if you look at the score models you have KPIs very well defined starting from level 1, 2, and 3, but when it comes down there are no standard way of KPIs.
It’s interesting when people talk about best practices, you can have best practices, but best practices for one of the customers, and one of the manufacturers, is completely different even if you make the same product, because that’s how operations is. And getting down into operations has always been a real challenge today, and I think the dissolving of the digital problem is, if you are able to solve your operational workflows and the movement of data out there, you are getting somewhere in digital Ken, that’s my firm belief.
You’ve actually been a perpetual thought leader from your days there at Schneider and Wonderware, and going on, and I love what you just describe because I think part of that was captured in some original work you did, ‘The Vision of the Perfect Plant, Coordination, Planning, Execution, Integration, and Intelligence’, and you wrote that in 2008. More recently I think you wrote a whitepaper for the World Economic Forum, and Cyber Resilience in the electricity ecosystem. I guess as I think about it, and I know you’ve written other things as well, in some sense those titles kind of describe the changing view of plant force systems, or as you say these operational systems in that sense. How has the definition of the perfect plant changed over the time that you’ve been writing these?
For the book I had co-authored two chapters of the ‘Perfect Plant’, and that’s the time where we were seeing the real timeliness, and that from the supply chain, you had the advanced planning and optimization, but to get real-time data on being able to reconfigure your inventory plans, you require that real-time data. Fast-forwarding it with the cybersecurity, very honored to have represented my company, we were part of a big working group committee where I contributed to the whitepaper, but looking at cybersecurity in the whole supply chain, you cannot look at cybersecurity today alone as an organization, if you really see what has changed over time.
So, big data, and I often say the biggest influence today started with big data, and the reason I say that is because if you compare big data and transaction data, big data is all about understanding the meaning behind the transaction data, and that today with the advent of IoT where you have this whole collection of million datapoints, you are really required to understand that. And today people don’t realize that everyone today is part of operations, whether they realize it or not, digital is all about business operations.
So, this whole concept about being perfect, if you look at the age-old consulting thing like AS-IS 2B I would say there isn’t any 2B today, there is no target reference to it because of the pace in technological advancement, there is no constant 2B, you have to be able to constantly look, validate your processes, you have to constantly look at agility. When I say agility, could I do a business process change today which would be effective three months into production, and out to the business, rather than the age-old 6-8 month or a year process?
So, that is where the perfectness of either an operation, or a manufacturing supply chain, the perfectness comes in adapting to the changes. A classic example today is COVID, post-COVID today, operations need to be either rigid and a different way of working, different way of doing things, decoupling and remoteness, that is where you really require the digital. So, in that sense the same principles from 10 years back are applicable today, but in the context of digital, the perfectness doesn’t have to be static, it is dynamic at every instance as we want today. That is where I see it.
It’s an interesting perspective, the no 2B, in some sense you could almost say it’s a perpetual 2B in the sense that you’re always agile and you’re always going to be adjusting if you will, whether that be ideal status in some sense.
Ideal status, and that is where the all DevOps movement with the whole containerization comes in, that now technology and IT, yeah, you cannot blame IT today but there are technology inventions today which are leading it into agility. And what is agility today, if a CEO says he wants to rejig say a supplier process, or if he wants to rejig on how manufacturing is done; by the time we look at process interventions, and technology interventions, what’s the time to value to deliver that. With age-old technology the time to deliver and value would be one year, today it could be 3 or 4 months and that could cost… that is your competitor advantage.
We’ve often observed in this podcast that digital industry as we like to call it, is driven in part by the virtualization of OT systems. So, you could think of it this way, industrial IoT as we call it is about virtual OT, or the virtualization of OT, such that if you think about the internet and cloud computing, what happened in IT over the last two decades has been the virtualization of traditional data centers into Sass and cloud services. To what degree do you believe this progress in IT is driving this perfect plant, or the perpetual 2B if you will of OT systems development?
Oh, this is what we have been thinking internally in our organization. But to me people are already doing virtualization, so virtualization the whole BPO industry, IT has been virtualized and that’s got into the whole hyper-converged infrastructure and architecture, with technologies like software defined networking. Coming down to where we are there’s rarely virtualization, you still have today and coming from the industrial automation world there are still soft PLCs applicable in machine shops, there are windows machines being used for real-time control. How do you take that scale? Today the hyper-scalers have been able to solve some of the problem in getting the response time down from seconds to milliseconds, and that is why if you see the investment today with all the hyper-scalers are being done at the edge.
So, at the end of the day I do see progress of this coming in very rapidly to this industry, and whoever distrusts this industry will be the lead follower. I always say, the million dollar question, is it possible to implement control functionalities, so if our control engineer has done PLC DCS, and all that, and is it possible to implement a control functionality on the cloud, employing a cloud infrastructure as a service with a comparable performance guaranteed, as that of a dedicated hardware based DC or PLC. There are pockets of research to be available where there are real-time virtualization engines, hypervisors which are available, low-latency deterministic network connectivity. And as this space and the ecosystem within the space have to figure out things which will help customers get there.
So, I would say that’s one of the big waves in OT waiting to happen, and whoever figures that out will have the leading advantage.
Yeah, we couldn’t agree more in terms of cloud coming down to the edge, and how that is impacting what you might say is the traditional IT/OT boundary, simply we’ll call it an IT/OT gap, we’ve used that term as well. Do you believe that the future holds an IT/OT boundary or gap? Or do you see that effectively disappearing as you truly go to – as I think you called it earlier, from shop to top, right?
Yes, so I would say the lines are blurring today, and the reason the lines are blurring today, is the convergence today is being fueled by data analytics decision making. And most importantly, the whole… I see this often, it’s the return of nerds, when I say the return of the nerds is we’ve been doing advance process controls, we’ve been doing simulation models, but now at the breadth and depth of scale of AI and ML, that is the driver for distributed federated control.
Just imagine today DCS, and that is where if we can think of autonomous control to be happening, why would I want to do cabling and bring it all to my DCS? Why do I have to have massive control rooms? You can have OEMs for turbines, or boilers, or any process equipment, have their edge controlling devices on containers, and you hook it up to a master cognitive control system sitting at a fog layer, or at the cloud layer, but ideally at the fog layer because then you have your traditional on-trend stuff where you can do local time control, but then give the training data to the cloud for you to train your models, just not for the asset.
When I say cognitive, it’s like, ‘Okay, Ashtad, what do you mean cognitive?’ I said, ‘Today all the predictive maintenance IoT use cases are revolved around an asset, you take that asset and you take that predictiveness and put it on the process in which the asset participates, that’s where you’ll start getting cognitive, and that’s the beauty of what I call the cognitive control system. So, I would say five or six years down the line, this would be a reality Ken.
We have an investment thesis we call, ‘Brown is the new green’, brownfield applications is where the real money is at, because nobody’s going to rip and replace their PLCs and put Arduino boards in there, at least not yet. But in some sense that overlay is that will invest in companies what we call the three E’s, it will embrace, extend, and ultimately exterminate those systems that they’re lying on top of, and DCS is a good architype for that. So, ultimately, we see the same thing happening, but it’s never going to move at the speed of Silicon Valley, or of enterprise IT. Because there’s real processes, real lives, real people, real productivity sitting at the other end of it.
Absolutely, and always if you see technology innovation, the embracing of technology, rapid technology innovation comes out of a financial market. So, I’ll give you an analogy, flash voice, the whole trading thing about trading stocks and getting your inputs from a stock market. If you think about real-time control, they require millisecond responses for them to trade. So, if that technology is being developed to get it to that segment easily in a millisecond and microsecond latency, architectures could be evolved down for control systems.
Exactly. The World Economic Forum we mentioned earlier, they’ve recently used the term called ‘The Great Reset’, and in several of our podcasts we’ve mentioned this in terms of referring to the long-term impact of COVID-19 pandemic. Given the futurist discussion we just had, what do you see as the impact of this on the future of OT and your own current business?
Yes, we see a de-risk including centralization, and decoupling starts becoming very important. So, if you see for risk mitigation companies might build a network of production facilities, leaving the long tradition of a single location large scale manufacturer. Offside operations, businesses will try to decouple onside and offside workforce, right source enabled by technology for business operations, and leverage service models for offside functions.
We’re seeing employment monitoring, surveys and technology will be used to know if their employers are workplace safe, thereby reducing the dependency of operations on such outbreaks. Automation and robotics were talking about that, but with social distancing becoming widespread, use of autonomous vehicles and robotics, reduced human-to-human contact is going to be very important. I was talking about cognitive control systems, so the next generation of industrial control systems will be designed to leverage the whole AIML to enable promote operations and ensure operational safety with minimum human involvement.
So, if you really see from a socio-economic aspect of what does it really mean, from digital things, take for instance small businesses around the world constitute around 40 to 60 percent of the GDP in most countries, yet many are cut off from the digital economy today. How do we as customers, manufacturers, or conglomerates just not look at what it’s going to be from a COVID perspective, it’s the whole supply chain of partners and the vendors you are dealing with, and can we take them along? So, for example, India, micro-economics are going to be very-very important, so for example microgrids for local power generation, for solar wind and batteries enabling small scale industries, that just create jobs and provide electricity to homes, schools, hospitals, and creating a self-sustaining ecosystem. Micro-education with education tools accessible on mobile devices, allowing schools to provide education without requiring training of millions of teachers.
So, this whole thing about micro-innovation, if you’re able to figure that out you already have the scale sitting out there. I think that is where real innovation is going to talk about in terms of… and that is why I again come back to why operational data is even more so important today than ever in this whole guise of digital journey.
Micro-innovation, there’s a new term, I’ll have to check if the trademarks are available, I love it! Pick-up the domain before we publish this, that’s a really good one! Of course, we’re digital industry investors and so we always like to ask the question in terms of recommendations of interesting startups, from your perspective who are the ones to watch out there, at least in this digital industry space?
I’m actually following Kelvin, Kelvin is an open industrial control system, but basically very innovative company, where they’re really having container-based approach to control systems, that’s one startup. Again, I come back to operations data, contextualizing operational data is a long sought-after thing especially for digital practitioners and data practitioners like myself. So, tailing off the operational data in context with the enterprise data, so Cognite is another startup, they have their fast platform which I’m very bullish about. And another cyber security company known as Xage based out of California, they’re actually a very innovative blockchain based approach to identity access management down at the controller level.
And I’m convinced, the investment in OT cybersecurity for the next five or six years is going to be tremendous, because that is where a lot of efforts are beginning. You can see just recently Microsoft bought CyberX an Israeli-based startup for IDS protection at the industrial control, ICS layer. So those are the three that come to mind.
Yeah, those are great ones. Our listening audience will appreciate that we are investors in Xage, and so we featured Duncan Greatwood on a webinar in the past, so good call on that one. We have been looking at the other two as well, so three great recommendations there, Kelvin, Cognite, and Xage. Final question, closing we always like to see if you can provide any recommendations of books or resources that inspire you.
The a16z Podcast, that’s one of my favorite podcasts of all time, that’s what I look forward to. There are other podcasts on Spotify or Pandora which is the Data Skeptic and the Data Engineering podcast. Because again, I do believe organizations if they can understand their data can have leapfrog advancements into their digital strategy. Another book which I like is, ‘The Grid’ by Gretchen Bakke, it talks about the whole grid in terms of the energy future, a great book to read. Another book is ‘Mindset’ by Carole Dweck. Today operational excellence is a mindset that starts with an individual, technology can help you adapt, but it’s all about integrated thinking, it’s about hey don’t copy the competition, but do that from other industries. So, it’s the how do you build that mindset and attitude. Another book which I like is ‘Life 3.0’ by Max Tegmark, its understanding the human aspect of interaction with artificial intelligence. Those are pretty much my books.
That nice heavy reading, I like that, and you’re the first to recommend the a16z podcast which I’m an avid listener to as well, it is great believe me. Well, Ashtad thank you so much for your insights, it’s been a pleasure to talk with another engineer, and especially you!
Hey, I get it all the time, customs, immigration, renewal of my driver’s license.
‘What do you do for a living Mr. Engineer?’!
I have my daughter becoming a doctor, so go figure it out, she’ll be called Doctor Engineer.
Yeah, medical technology I guess, Doctor Engineer, love it.
It’s a pleasure, thank you so much for having me.
Absolutely, we’ve really been pleased. So, this has been Ashtad Engineer, Head of Technology, Energy, and VP of Technology and Digitization at the Adani Group, and as I say, a lifelong cognitive digital industry leader. So, thank you for listening and please join us next week for episode 104 of our digital leadership podcast series, produced by, for, and about digital industry leaders. Thank you.
[End]