Momenta's Take: Automation to Autonomy: Will We Finally See “Lights Out” Factories?
Ken Forster
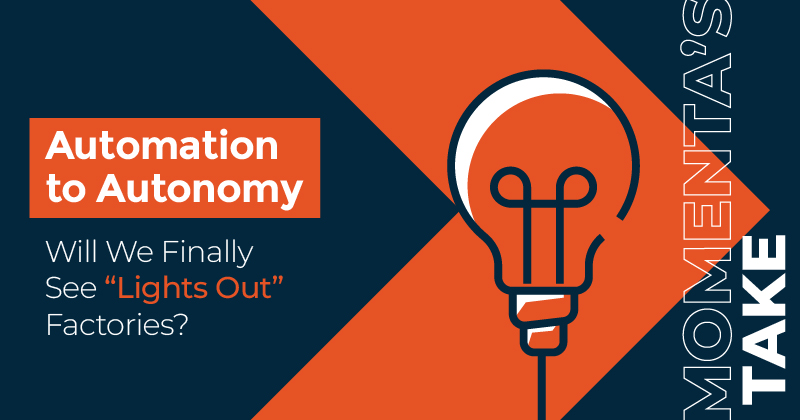
Automation to Autonomy - Will We Finally See “Lights Out” Factories?
The promise of fully autonomous systems continues to fuel innovation, most visibly around self-driving vehicles (including warehouse automation systems). The manufacturing sector has continued to invest in automation and technologies. The next stage of evolution will be to deploy autonomous workloads that can safely decide and act for themselves and enable operational efficiencies – by working alongside humans or taking humans completely out of the loop (allowing “lights out” operations).
The principles of Industry 4.0, combined with enabling technologies such as 5G connectivity, AI, AR/VR, edge computing, 3D printing, and advanced robotics, provide the foundation for factories that are self-learning, self-adjusting, self-healing, and capable of running on their own. “Lights-out manufacturing” refers to a methodology of fully automating the production of goods at factories and other industrial facilities so as to require no on-site human presence (a “Dark Factory”).
Continuous Pressures Compel Investments from Automation to Autonomy
The manufacturing sector faces significant pressures from the shortage of highly skilled workers, and the scarcity is reflected in increasing labor costs across the globe. The labor cost advantages of outsourcing manufacturing to Asia are receding as factory jobs become less attractive to younger workers, and businesses need to raise wages to compete.
The concerns over supply chain disruptions seen during the global pandemic and Ukraine war and rising transportation costs are also accelerating the trend toward re-shoring production back to developed countries (where wage and benefit costs are significantly more expensive). Additionally, despite extensive technological investments over the past decade, manufacturing productivity has surprisingly hit a plateau as organizations struggle with workforce challenges.
Getting to the Autonomous Factory
As manufacturing evolves from automated to autonomous systems, workflows must advance from running fixed, repetitive routines to becoming flexible and reactive. Combining artificial intelligence, machine learning, digital twins, simulation, robotics, and self-driving technologies can help advance manufacturing into the next stages of “hyper-automation” and eventual autonomy. Fully autonomous systems need to be self-controlling (being able to adapt as well as control), self-managing (able to automate analysis, decisions, execution, and maintenance), and most importantly, self-learning (able to improve and self-optimize over time).
Achieving fully autonomous “Lights Out” manufacturing requires several steps to realize, and manufacturers ultimately will need to pursue a maturity model that starts with data collection and incrementally integrates analysis, optimization, self-learning, and correction to eventually become a “system of systems.”
Source: Capgemini
Some Notable Use Cases, but Fully “Lights Out” Factories Still in the Future
There have been a number of historical efforts to deploy Dark Factories. IBM attempted its own in the 1980s but shuttered the effort because of an inability to respond to market changes. Apple built a similar plant in the1980s but closed it in the early 90s. In 2018, Tesla returned some of the automation at its fully automated Model 3 plant when machines failed to meet ambitious manufacturing targets. The most notable example of a successful “lights out” operation is Japanese robotics manufacturer FANUC (Fuji Automatic Numerical Control), which operates a dark facility where complex robots assemble other complex robots with zero human involvement in the manufacturing process.
There are a number of active use cases of autonomous processes in factories today. For instance, CNC machines can operate without continuous operator attention, and some machine shops can run jobs at night or on weekends. More practical autonomous use cases apply to specific processes within a larger operation. Many operations are implementing automated forklift technology. Europe’s largest pork processing plant in Denmark uses human labor to start the processing, and robotics quickly takes over.
A Chinese diesel automotive facility employs a more dark-factory approach to automate its assembly line fully. Integrating advanced analytics and Internet of Things (IoT) technology has also helped the facility use predictive maintenance to avoid equipment breakdowns. We expect increased adoption of autonomous processes at this stage, but human intervention will still be involved for practical, operational, and social reasons. Dark Factories, for now, remain a more aspirational model than near-term reality, but incremental advancements offer multi-faceted benefits.
Momenta is the leading Industrial Impact venture capital + growth firm. We accelerate entrepreneurs and leaders devoted to the digitization of energy, manufacturing, smart spaces, and supply chains. Since 2012, our team of deep industry operators have made over 100 investments in entrepreneurs and helped scale over 150 industry leaders via our award-winning executive search and strategic advisory practices.